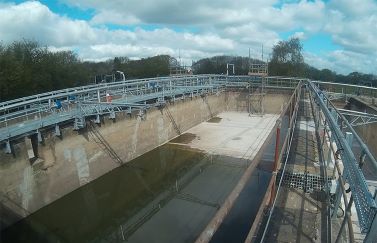
With all this rain we are experiencing at the moment, our drainage and sewage systems are having to work overtime, prompting us to look at stormwater attenuation tanks and how they are managed, in particular how they are cleaned to prevent them causing odour pollution.
Storm overfill tanks are being used more and more frequently. As climate change drives more extreme weather the number of times per year when the sewage system cannot cope with excess water is increasing. This means that storm tanks fill and empty more regularly and indeed more storm tanks are being commissioned into the UK’s water system
In addition, a current “hot topic” of focus for the environment agency seems to be the reduction of smell pollution. This means that storm tanks are being used more heavily at exactly the same time as the environment agency are insisting that any foul smelling residues be cleaned more thoroughly. Current methods of cleaning include:
- Tipping buckets
Large buckets of water are emptied into the tank from one end creating a wave that will remove debris from the bottom of the tank. - Eductor / swirl systems
These systems use a large educator nozzle to create a whirlpool as the tanks empty in an attempt to dislodged debris. - Manual cleaning
A human enters the tank with a pressure washer. - Impingement cleaners
A rotating nozzle head goes through an automated cleaning cycle bringing powerful cleaning jets to bare on each part of the tank.
THE CASE FOR IMPINGEMENT CLEANING
Impingement cleaning is by far the most water efficient method of cleaning a tank. This technology is not new but has been deployed for cleaning all manner of tanks and process vessels for decades. Most large chemical, petrochemical and food processing plants will have impingement tank cleaners as part of their vessel cleaning systems. This technology has been used with mixed results in the cleaning of storm tanks but has often run into problems for the following three reasons:
1- Scale
The size of tanks in the chemical and food industries are generally far smaller than storm tanks. A large process vessel may reach 7 or 8 meters in diameter but that is still pretty small for a storm tank. It is true that some of the larger petrochemical storage tanks reach storm tank size but none the less the cleaning systems generally deployed in in the process industry are cleaning much smaller areas.
2- Environment
Unlike the impingement cleaners deployed in the process industry, storm tank cleaning systems are not situated in a nice clean factory, lovingly tended and maintained by a team of process engineers. Instead they are left in a cold, dirty environments exposed to the elements which are largely unmanned most of the year. This environment means that any such system needs to be extremely rugged, more so than in other industries
3- Cleaning fluid quality
When cleaning chemical and food tanks a reliable supply of clean, filtered water is a given. Storm tank cleaning systems will often need to run on final effluent with a variable particulate content. This can place a significant strain on a cleaning system that is not designed to handle such poor quality cleaning fluids. What does this mean? This means that simply taking a process tank cleaner out of its “natural” environment and deploying it in a storm tank will not work. Some models on the market will have sufficient reach and power to clean large storm tanks but the tough environment and poor quality cleaning fluid will take their toll quickly, resulting in the machines clogging and breaking down. Typically these machines have an exposed gear system that can become gummed up with algae, silt or small bits of debris that somehow make it into the supply water.
LOOK TO THE SEAS! USING OIL TANKER CLEANING KNOW-HOW
So on the one hand we have a technology that can deliver more effective cleaning for less water and less cost and on the other we have known reliability issues when it is deployed. This is one of those situations that is simply begging for a solution. So what is the solution? The answer to this conundrum comes from a seemingly unlikely source, but it is one that, after a little reflection is entirely logical. The answer comes from the shipping industry and in particular the cleaning of oil tankers. Oil tankers need to be cleaned! Crude oil tends to form thick sticky layers of waxy residue over time and this impedes the carrying capacity of the tanker.
The problem is that oil residue is very hard to clean. Using water to clean these tankers creates a massive amount of oil/ water mix which needs to be filtered and disposed of. Furthermore water does not actually clean oil residue off very well (water and oil classically don’t mix!). The solution to this problem is to actually use crude oil as the cleaning fluid. Raw oil is put through high powered rotary jet cleaning systems to dislodge residue in the tanker and to give it a thorough clean. The tank is mostly emptied and then the remaining oil sludge / mud is circulated through the tank cleaning system. The very large solids that are removed are filtered out but the rest of the sludge is passed through the impingement tank cleaner. Clearly these tank cleaners need to be a bit of tougher beast than their counterparts deployed in say the food industry.
In addition to this, these tank cleaning systems need to remain in place unused for months at a time, often submerged in the crude oil in the tank. When not covered with crude oil they are exposed to the salty, corrosive marine environment. Cold, wet, exposed to the elements and very rarely even seen by a human being let alone maintained, is this environment starting to sound familiar? This technology has been deployed by all the world’s leading shipping and oil companies for over 40 years now. It is tried and tested technology and it is perfect for being redeployed to clean storm tanks.
How does it work? The principles of impingement jet cleaning are exactly the same as those in the food, pharmaceutical and chemical industries. Rotary jets spin through a set cleaning cycle bringing those jets to bare on each part of the tank, blasting away residue as the jet “explodes” outwards on impact. But there are key differences in the design of oil tanker cleaners when compared to process tank cleaners.
- Sealed gear box
One of the most important design features is the presence of a sealed greased gear box within the machine. Process industry tank cleaners are normally lubricated by the cleaning fluid with an exposed gear system. This is sensible in hygienic applications where contamination from lubricants is a considerable concern. In the oil tanker cleaning applications such contamination concerns are not present so a sealed lubricated gear box can be used. This then allows far more particulate to be passed through the tank cleaner with little or no risk of clogging the cleaner. - Tough design
When designing rotary tank cleaners for use in process vessels the focus is on creating a hygienic and self-cleaning machine. It needs to be polished and free from any nooks and crannies where contaminants or bacteria might hide. This inevitably means some sacrifices need to be made in ruggedness. In contrast ship cleaners have none of these concerns and so have been designed to be extraordinarily tough. This tough, rugged design is again perfect for use in cleaning storm tanks Large nozzles The big tanker cleaners will have 14, 16 or even 20 mm nozzles. These can throw a cleaning jet over 25 meters. Bear in mind that means a cleaning radius of 25 meters meaning a 50 meter diameter tank could be cleaned with a single machine. - Rough clean as opposed to precision
When cleaning a crude oil tanker it does not need to be spotless. As long as the vast majority of the residue is removed then the job is sufficient. In contrast, chemical and food tanks need to be completely cleaned. As such the cleaning patterns of process tank cleaners tend to be tighter requiring more rotations and more water. This is a waste in storm tanks because they simply do not need to be that clean. The level of cleaning required is very similar to that of oil tankers. Storm tanks don’t need to be spotless, they need to have enough residue removed so that it won’t start to stink and annoy the neighbours.
CONCLUSIONS
The redeployment of tanker cleaning technology to solve the problems of cleaning storm tanks is entirely logical. The environments that the ship cleaners need to operate in are probably tougher than anything they will be exposed to in storm tanks. They can handle dirty, particle contaminated cleaning fluids easily, they are relatively cheap to install and give by far the best cleaning of any method (with the possible exception of manned entry cleaning). In short, tanker cleaning technology represents a potential solution to storm tank cleaning problems.
For more information about storm attenuation tank cleaning, please call SNP on 01273 400092.