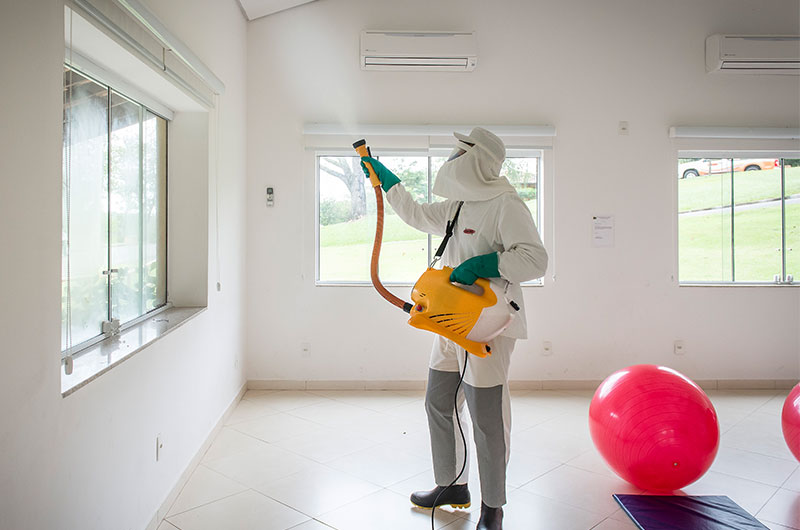
With the world slowly and tentatively coming out of coronavirus lockdown, businesses are thinking long and hard about how they will keep their workers safe. As we all return to work, employers have a heavy responsibility to ensure that workplaces are as safe as possible in this new “covid19 world” and part of these new safety protocols will be an increased need for cleaning and disinfection in the workplace. In order to get the world back to work effective cleaning and disinfection will be necessary on a regular basis both to protect employees and restore consumer confidence.
Most of this will be new for many businesses. This article looks at spraying/fogging for coronavirus and other pathogens purely from the perspective of spraying efficiency. It makes no attempt to comment on the effectiveness of the various types of antiviral disinfectants being used to combat the global pandemic. Instead I focus on the
mechanics of spraying/fogging and how we might go about selecting the correct nozzles and equipment.The basic principle – what we are looking to achieve in an ideal world
In an ideal world we need to get good contact between the antiviral agent and all places the virus may be lurking. A virus may be present in the air or on surfaces. As such, good contact time with the air along with a uniform coating of all surfaces would be ideal. This would be the perfect scenario.
Other considerations
Of course, in the real world we need to consider a variety of other things such as:
• Damage caused by the over wetting of surfaces
• Health risks posed by continued aerosolised disinfectants
• The cost of the spray dispersion system
• The time and manpower it takes to complete the process
These limiting factors need to be taken into account as does desire for the idealised “perfect” spray distribution system. For example, it would be great to be able to fog a room with a disinfecting mist that hangs around in the air for hours and at the same time slosh copious amounts of high strength disinfectant over all surfaces. This would definitely do a great job in making the environment safe from viral pathogens, but it might completely ruin the workplace and make it unsafe for people to work in for hours or even days due to the new chemical hazard introduced.
We should remember that end objective is NOT to kill the virus. It is to make the workplace safe for people to return to work in or receive clients and customers in. Killing the virus is not the end goal, a safe working environment is. It’s this subtle but important difference which will often mean some compromises from the ideal virus killing system.
Spray nozzle general function
Regardless of what the application is, a spray nozzle performs two functions: (1) It breaks apart a liquid into multiple droplets (atomisation). (2) It directs a liquid into a spray pattern. These are the two basic functions of all nozzles. Some applications only require fluid direction, some only require atomisation and some require both. Disinfection systems require both spray nozzle functions to varying degrees depending on the nature for the disinfection system.
Covid19 spraying specific requirements
As this is a new virus there are still may unknown factors. Research indicates that the main transmission mode of the virus is by direct human to human contact. Secondary transmission modes would seem to be through contact with contaminated surfaces and possibly, to a lesser degree, through contaminated air space.
Early studies would indicate that the virus is not truly airborne and that any viruses aerosolised by a cough or sneeze will rapidly settle out of the air. This means that entering an air space where an infected person has been coughing a short
period of time earlier will not increase the chance of infection by much. There is still a possibility of infection occurring in this way, but it diminishes very rapidly over time.
The survivability of the virus on surfaces, however, may be more problematic. Studies [1] have shown that the virus may remain viable for up to three days on surfaces. The rate of survival depends on the type of surface with hard shiny surfaces such as stainless steel and plastic having longer rates than porous surfaces like cardboard.
Whilst much is still unknown, it is becoming clear that the transmission of the virus by picking it up from surfaces is, in all likelihood, a far bigger problem than from the air. As such it is the disinfection of surfaces that would seem to be the priority.
Spray distribution
To disinfect work and public areas we need to treat both surfaces and air volumes. On a basic level we need to get the volume of disinfecting liquid in our container and distribute it over all surfaces and through air spaces so that it comes into contact with the pathogen we are trying to treat. Any spray nozzle being used will need to assist with this process. Secondary distribution processes may also be deployed, for example wiping to help spread the liquid over a surface or the use of fans to help distribute the spray around an air volume.
The role of atomisation & droplet size
Droplet size plays an important role in both the treatment of both air spaces and the formation of microsurface coatings on surfaces.
Airspaces
In order to treat airborne pathogens the disinfectant must remain airborne long enough to come into contact with the said pathogen. Large droplets will very rapidly fall out of the air and settle. Smaller droplets remain in the air for a much longer period of time. Very small droplets below about 10 microns in diameter will tend to remain airborne for a very long time as they will bounce from surfaces they come into contact with and not settle at all. This makes sub 10 micron, dry fogs highly suited to decontaminating air spaces of pathogens but, for obvious reasons, less suited for coating surfaces.
Surfaces
In order to treat surfaces the ideal scenario, as mentioned above, is to form a uniform coating on all areas. Obviously, a heavy spray will tend to coat anything it comes into contact with by soaking the entire surface but, as noted, this is far from efficient and far from practical in many real world situations.
Viruses generally only require a very small amount of disinfectant to kill them. The ideal coating scenario is to form a very thin micro layer of disinfectant on all surfaces. This is best achieved by finely atomised spray. If done correctly this has the further advantages of:
• Reducing chemical usage
• Reducing the health risk posed by these chemicals
• Reducing the chance of damage to electrical and other equipment sensitive to wetting
Droplet size and surface contact behaviour
When a droplet comes into contact with a surface a number of things can occur. It can bounce off, bounce and shatter, or adhere to the surface and spread out. What will happen depends on the speed of the droplet, the nature of the surface and the size of the droplet.
If a droplet is very large it will tend to shatter and bounce. Some of the liquid will adhere to the surface but it will be in quite a large pool. This will lead to a patchy and uneven coating on the surface. The surface will become wet and the only way to ensure an even and complete coating is by a secondary fluid distribution process like wiping. This is what happens when we spray a kitchen surface from a standard hand-held sprayer and then wipe down the surface. This is actually an excellent way to ensure a good coating of disinfectant on the surface but has serious practical limitations in terms of the labour and time required.
Smaller droplets will tend to form a much more even coating when they hit the surface. The small droplets will spread out and merge to form a layer. If we can atomise the spray enough then we can get close to the ideal of a very thin even coating. However, there is a sting in the tail to this approach. If we atomise the fluid too much then droplets will simply bounce off the surfaces.
Very small droplets below about 10 microns will tend to act more like solid particles or rubber balls than liquids. As such, they will simply bounce off surfaces.
This is particularly true if the surface is already a bit wet. This is excellent news if our aim is to keep the droplets airborne and to prevent all wetting, indeed the whole concept of dry fogging utilises this phenomenon, but it is not so good news if our aim is to generate a micro coating over all surfaces. Dry fogs will not adhere to surfaces and so will remain aerosolised for long periods of time meaning they are excellent at removing airborne pathogens, but they may not be the best for removing pathogens clinging to surfaces.
In addition to the fact that dry fogs will not adhere to surfaces the fact that they remain airborne for so long may also be problematic. The inhalation risk posed by aerosolised disinfectants means that the area may not be able to be entered safely for several hours. This may prove to be highly impractical if we are considering the widescale disinfection of public spaces.
Droplets size and spray distribution
Smaller droplets, however, do have their advantages. A sub 10-micron spray will remain airborne and will be carried around a room by air currents for a long time. The fact that it won’t settle out of the air means that it will reach every single nook and cranny in the room. In dry fogging operations this is, of course, the entire idea. The fog fills the room and reaches every part. This might not, however, be the idea scenario for the longer-term treatment of public places for covid19.
In an ideal world we want to leave a microlayer of disinfectant on every surface. This will not only kill the virus already present but will serve to kill any virus particles that are deposited after the spraying is completed. In public places a one-time fumigation will certainly kill off the virus already deposited but as soon as an infected person enters the space again it can become immediately re-contaminated. A residual layer of protection would be the ideal.
There are many disinfectant liquids that claim to deliver this residual effect. How well and for how long they work is beyond the scope and technical expertise of this author but what is clear is that, from a spraying perspective, the very fine sub 10-micron dry fogging applications of these chemicals will not be ideal. We do however need to ensure the chemicals reach every area and so do still need good atomisation. As such, a balancing act may be required.
The balancing act
On the one hand we need good atomisation, so the liquid remains airborne long enough to be carried to every nook and cranny. On the other hand, we don’t want to atomise the fluid so much that it does not adhere to surfaces. Furthermore, we do not want the disinfectant to remain airborne for too long as this might mean the public space is unable to be entered for many hours. Logic would dictate that perhaps droplets in the 15-30 micron range might be more appropriate.
Indeed, several studies have come to this conclusion. A 1999 study by Burfoot et Al [2] modelled the likely distribution of 5, 15 and 35 micrometre droplets. The models showed that whilst the 5 micron droplets gave a good even coating in the whole room, they would remain airborne for too long. In contrast the 35 micrometre droplets would settle quickly but quite locally. The 15 micron droplets offered a happy medium. Another study published 201 concluded that if droplets were to large surface coverage would be poor and wetting would be problematic but if they were to small droplets may not penetrate the surface and remain airborne for too long. [3]
Getting the best of both worlds
The use of mobile fogging systems may help to get the best of both worlds. If the source of the fog can be directed and moved so that it can be brought to the vicinity of all surfaces then a more even micro coating may be achievable. A fog with a droplet size of 30 microns will probably not fair too well if it is required to cover all areas of a room from a single point but would be a good droplet size if it can be manually directed close to the surface being treated. Indeed, the quicker settling time of larger droplets may be advantageous as the room being cleaned will not remain hazardous to enter for so long. It should be noted that even 30 micron fogs applied locally with care will not produce significant wetting and so damage to sensitive surfaces can still be avoided with fogs of this nature.
Spray nozzle choices
There are two broad types of spray nozzle that would seem ideal:
High pressure hydraulic
High pressure misting nozzles will tend to operate at pressures between 20 and 100 bar. Within this pressure range droplet sizes of between 15 and 100 microns are achievable. The higher the pressure the lower the droplet size for any given nozzle. It is also true that flow rates will increase with pressure. This being the case it can sometimes be hard to balance the correct flow rate required with the droplet size
required.
A further problem with simple hydraulic misting nozzles is that the sprays they
produce tend to lose momentum at a short distance from the nozzle. Even at high pressures most of the energy from the pump is used to atomise the fluid (this is what the nozzles are designed for) so even though the exit velocity from the orifice will be very high the small droplets will very rapidly slow and within 10cm or so from the nozzle they are effectively under the direction of air currents.
This means that the use of hydraulic misting nozzles to treat large areas requires some kind of secondary fluid distribution system. This is normally in the form of a fan to blow the fog where it is needed.
Air atomising nozzles
These nozzles mix fluid and air to form a fine mist or fog. In addition to atomising the fluid the presence of compressed air in the mix helps distribute and carry the resulting spray. Air atomisers can throw a plume of fog several meters from the nozzle. They can fairly rapidly fill a room with a fog/mist of fine droplets in the 25 micron average droplet range. These droplets will move around via air currents to get to every nook and cranny but will adhere to surfaces when they contact them. As such, air atomiser nozzles may be a good choice of fogging systems.
Conclusions
A balancing act between the small droplet sizes needed for good, even distribution and their ability to quickly settle out of the air and adhere to surfaces needs to be found.
Droplets below 10 microns in size are unlikely to be optimal for disinfecting surfaces. They will be excellent for disinfecting air spaces and will remain airborne for hours. This may mean they are impractical for public space fumigation due to being an ongoing hazard to health.
Droplets between 10 and 25 microns will settle out of the air fairly quickly but will still have good distribution around a room from a single point fogging system.
Droplets above 25 microns are unlikely to be optimal for distribution from a single point fogger but would be suitable for mobile foggers that can be directed where needed i.e. solving the distribution limitations.
Droplets above 60 microns are likely to cause significant wetting and should be considered as a spray rather than a fog. They will be effective in disinfecting but will require more fluid in order to get a complete coating and will need to be applied locally by mobile sprayers. Research shows that this may offer additional benefits in mechanical action cleaning and penetrating biofilms especially when combined with wiping. [4] Whilst single point fogging systems that are simply turned on and left to fog the whole room are very attractive from a labour saving and operator safety point of view they may not be ideal for all situations. For smaller areas they would be an excellent choice but for larger and more complex areas manual, directed fogging systems will probably get better results.
A final conclusion is that much more empirical research needs to be conducted in this area. The above essay is the perspectives of a spray engineer trying to objectively think about this as a fluid distribution problem. There may well be subtle nuances due to a complex interplay between the different chemicals used, their evaporation rates, stickiness and the contact time required to kill pathogens. These factors may well
affect spray nozzle selection and I confess that this is beyond my own expertise.
What I would dearly like to see is actual empirical trials carried out by independent bodies in realistic experimental set ups that mimic the complexities of spraying in the real world. A comparative study between different spray methods would be great to see. This would give some excellent and much needed data. Much of the past search is limited in scope and one is left to piece together a picture of what is best to advise. The above is my attempt to do this in an as objective way as possible.
Appendix 1 – Summary of drop size properties
References
[1] Doremalen et al, Aerosol and Surface Stability of SARS-CoV-2 as Compared with SARS-CoV-1 The New England Journal of Medicine
[2] D Burfoot et al, Fogging for the disinfection of food processing factories and equipment, Trends in Food Science & Technology Volume 10, Issues 6–7, June 1999, Pages 205-210
[4] Bolton et al, Sanitizer efficacy against murine norovirus, a surrogate for human norovirus, on stainless steel surfaces when using three application methods, Appl Environ Microbiol. 2013 Feb;79(4):1368-77. doi: 10.1128/AEM.02843-12. Epub 2012 Dec 21.
Ivan Zytynski
Spray People Group
May 2020